Vibratory Feeders vs. Screens: A Comprehensive Comparison
In various industries, material handling and processing are critical to operational efficiency and productivity. Two commonly used pieces of equipment in this domain are vibratory feeders and vibratory screens. Understanding the differences and applications of these two systems can help businesses make informed decisions when selecting the right equipment for their needs. This article delves into the characteristics, advantages, and applications of vibratory feeders and screens, offering a comprehensive comparison to aid in the decision-making process. Vibratory Feeders vs. Screens
Understanding Vibratory Feeders
Vibratory feeders are devices that utilize vibrations to move bulk materials from one point to another. These machines play a vital role in various industries, including manufacturing, mining, and food processing.
How Vibratory Feeders Work
Vibratory feeders consist of a trough or a conveyor system that vibrates to transport materials. The vibration is generated by an electromagnetic or electromechanical drive, creating a consistent and controlled flow of material. The angle of the trough can often be adjusted to optimize the flow rate and material handling efficiency.
Types of Vibratory Feeders
There are several types of vibratory feeders, including:
Electromagnetic Feeders: These feeders use electromagnetic drives to produce vibration, allowing for precise control over the material flow.
Mechanical Feeders: Powered by mechanical drive systems, these feeders are suitable for larger material handling applications and can handle heavier loads.
Rotary Feeders: Designed for bulk materials, these feeders use rotating paddles or blades to move materials through the system.
Advantages of Vibratory Feeders
Vibratory feeders offer several benefits that make them a popular choice in various applications:
Consistent Material Flow
Vibratory feeders provide a steady and controlled flow of materials, ensuring that downstream processes operate smoothly and efficiently. This consistency is crucial in applications where precise measurements are required.
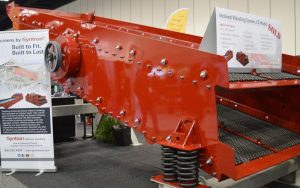
Versatility
These feeders can handle a wide range of materials, including powders, granules, and bulk solids, making them suitable for various industries. Their versatility enables them to adapt to different material characteristics and operational requirements.
Minimal Maintenance
With fewer moving parts compared to other conveying systems, vibratory feeders require minimal maintenance. This feature reduces downtime and operational costs, allowing businesses to focus on productivity.
Understanding Vibratory Screens
Vibratory screens, on the other hand, are used primarily for the separation and classification of materials. These machines utilize vibrations to sift materials based on size, allowing for efficient screening processes.
How Vibratory Screens Work
Vibratory screens consist of a series of screens or sieves that vibrate to separate materials by size. The vibration causes the material to move across the screen surface, allowing smaller particles to pass through while larger particles remain on top. https://industrialvibration.com.au/
Types of Vibratory Screens
There are several types of vibratory screens, including:
Linear Vibrating Screens: These screens produce a linear motion to separate materials efficiently.
Circular Vibrating Screens: Utilizing circular motion, these screens are effective for separating materials with varying sizes and densities.
High-Frequency Screens: Designed for fine particle separation, high-frequency screens utilize higher vibration frequencies to improve efficiency.
Advantages of Vibratory Screens
Vibratory screens offer numerous advantages that make them essential in various processing operations:
Efficient Separation
Vibratory screens provide highly efficient separation of materials based on size, allowing for better material classification. This efficiency improves product quality and reduces waste in processing operations.
Customizable Screening Solutions
Vibratory screens can be customized with different screen sizes, mesh types, and configurations to suit specific material handling needs. This adaptability enables businesses to optimize their screening processes for various applications.
Enhanced Material Recovery
By effectively separating and classifying materials, vibratory screens enhance material recovery rates. This improvement can lead to cost savings and increased profitability in processing operations.
Comparing Vibratory Feeders and Screens
While both vibratory feeders and screens utilize vibrations in their operation, their functions and applications differ significantly.
Functionality
Vibratory feeders are designed primarily for material handling and transportation, ensuring a consistent flow of materials to downstream processes. In contrast, vibratory screens focus on separating materials based on size, making them essential for classification and sorting.
Application Areas
Vibratory feeders are commonly used in industries such as food processing, pharmaceuticals, and mining, where material flow control is crucial. Vibratory screens are prevalent in aggregate, recycling, and mining industries, where efficient separation of materials is required.
Operational Considerations
When choosing between vibratory feeders and screens, consider the specific operational requirements. For applications that prioritize material flow and transportation, vibratory feeders are ideal. For processes requiring separation and classification, vibratory screens are the preferred choice.
Choosing the Right Equipment
Selecting the appropriate equipment for material handling and processing involves evaluating several factors:
Material Characteristics
Consider the type, size, and weight of the materials being handled. Different feeders and screens are designed to accommodate specific material properties, making it essential to choose equipment that aligns with your operational needs.
Throughput Requirements
Evaluate the required throughput for your operation. Understanding the volume of material to be processed will help determine the appropriate size and type of feeder or screen needed.
Space and Layout Constraints
Assess the available space and layout for equipment installation. Vibratory feeders and screens come in various sizes and configurations, so it is crucial to choose options that fit within your facility’s constraints.
Conclusion
In summary, both vibratory feeders and vibratory screens play essential roles in material handling and processing. While feeders focus on moving materials efficiently, screens excel in separating and classifying them. Understanding the differences between these two systems is vital for making informed decisions that enhance operational efficiency. By considering factors such as material characteristics, throughput requirements, and space constraints, businesses can select the right equipment to meet their specific needs and drive productivity in their operations.