Choosing the Right Mining Vibrator
Selecting the correct mining vibrator is crucial for ensuring efficient operations, preventing material flow issues, and enhancing productivity. With numerous options available, understanding your specific requirements can simplify the selection process and help you invest in the most suitable equipment.
This guide explores the factors to consider, types of mining vibrators, and practical tips for making an informed choice.
Why Mining Vibrators Are Essential
Mining vibrators play a vital role in streamlining material handling, preventing blockages, and improving processing efficiency. They are indispensable for various applications such as hoppers, chutes, conveyors, and vibratory screens.
Key Functions of Mining Vibrators
Material Flow Management: Keep materials moving steadily, preventing clogs.
Screening and Sorting: Facilitate separation of materials by size and type.
Feeding Systems: Ensure a consistent supply of materials to crushers or mills.
Dewatering Applications: Remove excess moisture for better handling.
Factors to Consider When Choosing a Mining Vibrator
Material Characteristics
Understanding the properties of the materials being processed is critical. Consider:
Material Density: Heavier materials require vibrators with higher force output.
Particle Size: Fine materials may need higher frequency vibrators, while coarse materials benefit from lower frequencies.
Moisture Content: Sticky or wet materials require vibrators with strong amplitude to prevent buildup.
Application Requirements
Evaluate the specific application to determine the vibrator type and performance needed:
Flow Rate: Ensure the vibrator can handle the required material flow volume.
Mounting Location: Assess the structure where the vibrator will be installed.
Operational Environment: Consider factors like temperature, dust, and vibration tolerance. https://industrialvibration.com.au/product/pneumatic-roller-vibrator/
Power Source Availability
Mining vibrators come in electric, hydraulic, and pneumatic variants. Choose based on the available power infrastructure:
Electric Vibrators: Reliable and widely used. Ideal for fixed installations.
Hydraulic Vibrators: Suitable for heavy-duty applications and high force requirements.
Pneumatic Vibrators: Lightweight and portable, ideal for temporary or small-scale applications.
Vibration Frequency and Amplitude
Frequency: Determines how quickly the vibrator oscillates. High-frequency vibrators are ideal for light, fine materials.
Amplitude: Refers to the intensity of vibration. High amplitude is necessary for heavy, dense materials.
Types of Mining Vibrators
Rotary Vibrators
These use rotary motion to create vibrations and are effective in compact areas. They are commonly used in feeders and conveyors.
Electromagnetic Vibrators
Offering precise control over vibration intensity and frequency, these vibrators are ideal for delicate materials and controlled flow.
Pneumatic Vibrators
Powered by compressed air, they are lightweight and versatile, making them suitable for portable applications.
Hydraulic Vibrators
Designed for demanding operations, hydraulic vibrators deliver high power and are well-suited for large-scale mining projects.
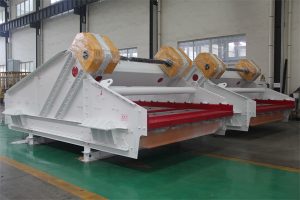
Steps to Choose the Right Mining Vibrator
1. Identify Your Application Needs
Start by understanding the specific requirements of your mining operation. Define the material type, flow rate, and environmental conditions to narrow down options.
2. Consult Manufacturer Specifications
Review technical details such as force output, frequency range, and power consumption. Compare these with your operational demands.
3. Evaluate Durability and Maintenance
Choose vibrators built to withstand harsh mining conditions. Opt for models that are easy to maintain and have readily available replacement parts.
4. Test for Compatibility
If possible, conduct a trial run to ensure the vibrator integrates seamlessly into your existing setup without causing disruptions.
Common Mistakes to Avoid
Overlooking Material Properties
Choosing a vibrator without considering material density, size, or moisture content can lead to inefficiencies.
Ignoring Power Compatibility
Selecting a vibrator incompatible with the available power source can result in operational delays or costly modifications.
Focusing Solely on Price
While cost is important, prioritize durability and performance to avoid frequent replacements or downtime.
Tips for Maintaining Mining Vibrators
Regular Inspections
Schedule routine checks to identify signs of wear, loose connections, or mounting issues.
Proper Lubrication
Ensure all moving parts are adequately lubricated to reduce friction and extend the equipment’s lifespan.
Calibrate Settings
Periodically review and adjust frequency and amplitude settings to maintain optimal performance. For turbine vibrators, see here.
Replace Damaged Components
Promptly replace worn-out or damaged parts to avoid disruptions in operations.
Future Trends in Mining Vibrators
Smart Technology
IoT-enabled vibrators provide real-time monitoring and predictive maintenance, reducing downtime.
Energy Efficiency
Manufacturers are designing vibrators with lower energy consumption to minimize operational costs and environmental impact.
Customization Options
Tailored solutions for specific mining applications are becoming more common, allowing operators to maximize efficiency.
Conclusion
Choosing the right mining vibrator is essential for efficient, safe, and cost-effective operations. By understanding your material properties, application requirements, and environmental factors, you can select a vibrator that meets your needs and enhances productivity.
Invest in quality vibrators, follow best practices for installation and maintenance, and keep up with technological advancements to ensure long-term success in your mining endeavors.