The Role of Vibrators in Manufacturing: Enhancing Efficiency and Precision
Vibrators play a significant role in modern manufacturing processes by improving efficiency, consistency, and precision. From material handling and sorting to compaction and testing, vibrators are integral in numerous applications. As manufacturing industries strive for higher productivity and cost-effectiveness, the role of vibrators has become more critical than ever. In this article, we will explore the importance of vibrators in manufacturing, their various types, and how they contribute to enhancing overall performance.
Understanding Vibrators in Manufacturing
What Are Vibrators in Manufacturing?
Vibrators are mechanical devices designed to generate controlled vibrations. In manufacturing, these vibrations are used to achieve various objectives such as material movement, compaction, separation, and even testing. By utilizing vibratory motion, these devices help streamline processes that involve the handling or manipulation of bulk materials, ensuring consistent, reliable, and efficient operations.
In manufacturing settings, vibrators are commonly used in equipment such as hoppers, conveyors, screens, and feeders. They help to move materials, compact powders or aggregates, prevent material clumping, and even facilitate sorting or sieving.
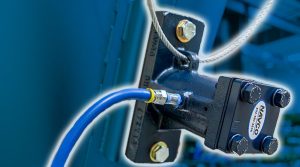
Key Applications of Vibrators in Manufacturing
Vibrators are employed in various manufacturing processes, including:
- Material Handling: Ensuring that materials flow smoothly through conveyors, hoppers, and chutes.
- Sieving and Screening: Helping to separate materials by size, ensuring uniformity and consistency.
- Compaction: Compressing materials like concrete, sand, or powders for improved density and quality.
- Feeding Systems: Ensuring consistent and uniform delivery of materials or components in assembly lines.
- Testing and Quality Control: Vibrators are used in testing laboratories for stress testing and material analysis.
Types of Vibrators Used in Manufacturing
Electromechanical Vibrators
Electromechanical vibrators are one of the most common types used in manufacturing. These vibrators work by converting electrical energy into mechanical vibration through an electric motor and eccentric weights. They are ideal for applications requiring a continuous and stable vibration pattern, such as material flow, separation, and compacting.
Features of Electromechanical Vibrators
- Continuous Operation: They can run continuously without overheating, making them ideal for long-term use in manufacturing.
- Adjustable Frequency and Amplitude: Operators can control the frequency and amplitude of vibrations to suit different applications.
- Durable and Reliable: These vibrators are known for their longevity and reliability in harsh industrial environments.
Pneumatic Vibrators
Pneumatic vibrators use compressed air to generate vibrations. These vibrators are particularly useful in environments where electrical components cannot be used, such as in hazardous or explosive environments. Pneumatic vibrators are also used when high-frequency vibrations are required, such as in vibrating sieves or screening machines.
Advantages of Pneumatic Vibrators
- High Frequency: Pneumatic vibrators are capable of producing high-frequency vibrations, ideal for fine powders or delicate materials.
- Explosion-Proof: These vibrators are safe for use in environments with flammable materials or gases.
- Minimal Maintenance: With fewer moving parts, pneumatic vibrators require less maintenance compared to other types.
Hydraulic Vibrators
Hydraulic vibrators operate using hydraulic power to create vibrations. These vibrators are typically used in applications that require high-force vibration, such as compacting large volumes of concrete or aggregates. Hydraulic vibrators provide precise control over the vibration intensity, making them suitable for applications requiring powerful and adjustable forces.
Features of Hydraulic Vibrators
- High Force Output: Hydraulic vibrators deliver powerful vibrations, ideal for compacting large amounts of material.
- Adjustable Control: The vibration intensity can be adjusted to suit specific tasks, ensuring optimal performance.
- Durability: These vibrators are built to withstand harsh conditions, making them suitable for heavy-duty applications.
How Vibrators Enhance Manufacturing Processes
Improving Material Flow and Handling
One of the most critical functions of vibrators in manufacturing is improving material flow and handling. Bulk materials, such as powders, aggregates, or granules, can often become stuck, clumped, or bridged inside hoppers or chutes. Vibrators help overcome these challenges by introducing controlled vibrations that keep materials flowing smoothly and continuously.
For example, in an automated assembly line, vibrators ensure that components or parts are fed evenly and consistently into the production process. In material handling, they help prevent blockages in chutes and conveyors, allowing the process to continue without interruptions.
Benefits of Vibrators in Material Handling
- Prevents Blockages: Vibrators keep materials from clumping, ensuring continuous flow through systems like hoppers and chutes.
- Increases Efficiency: With materials flowing smoothly, manufacturing processes become more efficient, reducing delays and downtime.
- Improves Storage and Distribution: Vibrators can also help compact materials to maximize storage space and improve their distribution across production lines.
Ensuring Consistent Compaction
Compaction is essential in manufacturing processes that require a uniform material structure or density, such as concrete production, powder processing, and even in industries like food processing. Vibrators are used to compact materials by removing air pockets and ensuring consistent density.
In concrete manufacturing, vibrators ensure that the mixture is properly compacted to form a solid and durable end product. Similarly, in powder or granule processing, vibrators help achieve consistent compaction, improving the final product’s quality.
Benefits of Vibrators in Compaction
- Uniform Density: Vibrators help achieve a uniform material density, improving the quality and durability of the final product.
- Faster Processing: Vibrators expedite the compaction process, reducing production time.
- Reduced Waste: Proper compaction ensures that materials are used efficiently, reducing waste and improving cost-effectiveness.
Enhancing Sieving and Sorting
Vibrators are also essential in sieving and sorting applications. In industries like pharmaceuticals, food production, and mining, vibrators are used to separate materials by size or quality. Vibratory sieves or screening machines help sort materials quickly and accurately, improving product consistency and quality.
Vibrators ensure that sieving or sorting operations are efficient by preventing clumping and ensuring materials pass through screens or sieves without blockage. This is especially important when dealing with fine powders, granular materials, or delicate components that need to be sorted precisely.
Benefits of Vibrators in Sieving and Sorting
- Accurate Separation: Vibrators provide consistent motion, ensuring that materials are separated by size or quality accurately.
- Increased Productivity: The use of vibrators speeds up the sieving and sorting process, boosting production rates.
- Enhanced Quality Control: Vibrators ensure that only the desired materials are selected, improving the overall quality of the final product.
Optimizing Testing and Quality Control
In manufacturing, testing and quality control are crucial for ensuring that products meet industry standards and customer expectations. Vibrators are used in testing applications such as vibration testing, stress testing, and material testing.
For example, in the automotive industry, vibrators simulate road conditions to test the durability of parts or assemblies. In material testing, vibrators can be used to analyze the performance of materials under different conditions, ensuring they meet the required specifications.
Benefits of Vibrators in Testing and Quality Control
- Simulated Testing: Vibrators allow for accurate simulation of real-world conditions, helping to identify potential issues before production.
- Improved Product Quality: Consistent vibration helps manufacturers identify weaknesses in materials or components, leading to higher-quality products.
- Time and Cost Savings: By detecting issues early in the testing phase, manufacturers can avoid costly errors during production.
The Future of Vibrators in Manufacturing
As manufacturing processes become increasingly automated and precise, the role of vibrators will continue to grow. The ongoing development of smarter and more energy-efficient vibrators will help manufacturers improve performance, reduce costs, and increase productivity. Innovations in technology, such as IoT integration and machine learning, will allow for more advanced control of vibrators, enabling operators to optimize vibration parameters in real time.
In conclusion, vibrators are essential components in modern manufacturing, contributing to improved material handling, compaction, sorting, and testing. Their ability to increase efficiency, improve product quality, and reduce downtime makes them an indispensable tool across various industries. As technology continues to advance, the role of vibrators in manufacturing will become even more significant, driving further improvements in operational efficiency and productivity.