Top Mining Vibrator Innovations
Mining vibrators play an essential role in ensuring efficient material handling, processing, and transportation within mining operations. Over the years, innovations in mining vibrator technology have significantly improved their performance, reliability, and efficiency. In this article, we will explore the top mining vibrator innovations that are shaping the future of the mining industry, enhancing productivity, and reducing operational costs.
Understanding the Role of Mining Vibrators
Mining vibrators are primarily used to facilitate material movement in various mining operations. They are critical in applications such as material flow, screening, separation, and feeding systems. By creating vibrations, these devices help in preventing blockages, ensuring continuous material flow, and reducing downtime. They are found in equipment like hoppers, chutes, conveyors, and vibrating screens, ensuring that materials move smoothly from one point to another.
While traditional mining vibrators have served their purpose well over the years, recent innovations have introduced more advanced features that optimize mining processes. Let’s take a closer look at these innovations and how they are revolutionizing the mining industry.
Innovations in Mining Vibrator Technology
As the mining industry evolves, so does the technology that supports it. Mining vibrator manufacturers have been at the forefront of innovation, introducing new features that increase efficiency, safety, and sustainability. Some of the top mining vibrator innovations include:
1. Smart Vibration Control Systems
One of the most significant innovations in mining vibrators is the integration of smart vibration control systems. These systems use sensors and advanced algorithms to continuously monitor the performance of vibrators and adjust vibration intensity in real-time. Smart vibration control systems can optimize the flow of materials, reduce energy consumption, and minimize wear and tear on equipment. By automatically adjusting vibration levels, these systems ensure that the right amount of vibration is applied, preventing over- or under-vibration, which can lead to inefficiencies or damage to the equipment.
2. High-Efficiency Electric Vibrators
Energy efficiency is a top priority in modern mining operations, and high-efficiency electric vibrators are leading the way. Unlike traditional pneumatic or hydraulic vibrators, electric vibrators are more energy-efficient, requiring less power to generate the same level of vibration. These vibrators are designed to consume less energy while delivering optimal performance. They can be easily integrated into existing mining equipment and provide consistent and reliable vibration for material flow and screening. The use of high-efficiency electric vibrators also reduces operational costs and carbon footprints, making them a more sustainable choice for mining operations.
3. Pneumatic and Hydraulic Hybrid Vibrators
Pneumatic and hydraulic vibrators are commonly used in the mining industry, but recent innovations have led to the development of hybrid systems that combine the benefits of both power sources. Pneumatic and hydraulic hybrid vibrators offer increased power and reliability while maintaining energy efficiency. These systems are particularly useful in heavy-duty mining applications, such as large-scale ore handling or materials with high-density properties. Hybrid systems allow for more precise control of vibration intensity and improve performance in applications where traditional pneumatic or hydraulic vibrators might fall short.
4. Wireless Remote Control for Vibrators
Wireless remote control systems for vibrators are becoming increasingly popular in mining operations. These systems allow operators to control vibrators from a distance, providing greater flexibility and safety. With wireless remote control, operators can adjust vibration levels and monitor the performance of vibrators in real time without having to be in close proximity to the equipment. This innovation is especially useful in hazardous environments or when vibrators are located in hard-to-reach areas. Wireless control systems improve operational efficiency, reduce downtime, and enhance safety on the job site.
5. Self-Cleaning Vibrators
One of the challenges in mining operations is the accumulation of dust, debris, and material build-up on equipment. Traditional vibrators can become clogged or obstructed, reducing their performance and efficiency. To address this issue, self-cleaning vibrators have been developed. These vibrators feature an integrated cleaning mechanism that prevents material buildup on the vibrator’s surface. By keeping the vibrator clean, these systems ensure continuous and uninterrupted operation, reducing downtime and maintenance costs. Self-cleaning vibrators are particularly beneficial in mining applications involving sticky or wet materials, which are prone to clogging.
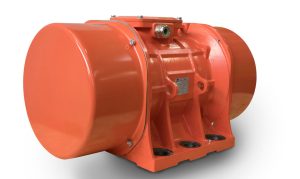
6. Vibrators with Modular Design
The modular design of modern mining vibrators is another innovation that is gaining traction in the industry. Modular vibrators are made up of interchangeable components that can be easily replaced or upgraded. This design allows for greater flexibility, as operators can customize vibrators to meet the specific needs of their mining operations. Modular vibrators are easier to maintain, as worn-out parts can be replaced without needing to replace the entire unit. This innovation reduces maintenance costs and extends the lifespan of vibrator equipment.
Benefits of Mining Vibrator Innovations
The innovations in mining vibrator technology have brought numerous benefits to the mining industry. Let’s look at some of the key advantages of these advancements.
1. Enhanced Efficiency
The integration of smart vibration control systems, energy-efficient electric vibrators, and hybrid pneumatic and hydraulic vibrators has significantly improved the efficiency of mining operations. These innovations ensure that vibrators work optimally, reducing unnecessary power consumption while maintaining consistent material flow. Enhanced efficiency leads to faster processing times, reduced material handling costs, and greater productivity.
2. Reduced Energy Consumption
Energy efficiency is one of the most important considerations in modern mining operations. The development of high-efficiency electric vibrators and hybrid pneumatic and hydraulic vibrators has led to significant energy savings. By using less power to generate the same level of vibration, these innovations help reduce operational costs and minimize the environmental impact of mining activities.
3. Increased Safety
Wireless remote control systems and self-cleaning vibrators have contributed to improved safety in mining operations. Remote control allows operators to adjust and monitor vibrators without being in close proximity to the equipment, reducing the risk of accidents. Self-cleaning vibrators help prevent material build-up that could cause malfunction or hazardous conditions. Together, these innovations enhance worker safety and reduce the likelihood of injury.
4. Reduced Maintenance Costs
The modular design of vibrators, combined with self-cleaning mechanisms and improved durability, has helped reduce maintenance costs in mining operations. Operators no longer need to replace entire vibrator units when parts wear out. Instead, they can simply replace individual components, extending the lifespan of the equipment. This reduces downtime and keeps maintenance costs low.
Choosing the Right Mining Vibrator Innovation for Your Operation
When selecting a vibrator for your mining operation, it’s important to consider the specific needs of your operation. Here are some factors to keep in mind when choosing the right vibrator innovation:
1. Material Type
Consider the type of material you are handling. Some vibrators are better suited for heavy-duty materials like ores and coal, while others are more effective for finer materials. High-efficiency vibrators may be ideal for lighter materials, while hydraulic or hybrid vibrators may be better for dense or sticky materials.
2. Power Requirements
Evaluate the power requirements of your mining operation. If energy efficiency is a priority, electric vibrators or hybrid models may be the best option. For heavy-duty applications, hydraulic vibrators may provide the power you need to ensure reliable material flow. https://mine.nridigital.com/mine_australia_may19/oli_vibrators_company_insight
3. Operational Environment
Consider the operational environment, including the accessibility of vibrators and safety concerns. If your operation involves hazardous conditions, wireless remote control systems and self-cleaning vibrators may be essential for reducing risk and improving efficiency.
Conclusion
Mining vibrator innovations have transformed the industry, bringing advancements in efficiency, energy savings, safety, and maintenance. Smart vibration control systems, high-efficiency electric vibrators, hybrid models, and wireless controls are just a few examples of how technology is enhancing the performance of mining equipment. By selecting the right vibrator for your operation and embracing these innovations, you can improve productivity, reduce costs, and ensure a safer, more efficient mining process.