Understanding Roller Vibration: Causes and Solutions
Roller vibration is a common issue in industrial machinery, affecting the efficiency and longevity of equipment. Understanding the causes and solutions of roller vibration is crucial for maintaining smooth operations. This article explores the primary reasons behind roller vibration and offers practical solutions to mitigate its impact.
Causes of Roller Vibration
Vibrations in rollers can stem from various factors. Identifying the root cause is essential for effective troubleshooting and maintenance.
1. Imbalance in the Roller
One of the most common causes of roller vibration is an imbalance. This occurs when the roller’s mass distribution is uneven, leading to centrifugal forces during rotation. Imbalances can be due to manufacturing defects, material buildup, or wear and tear over time.
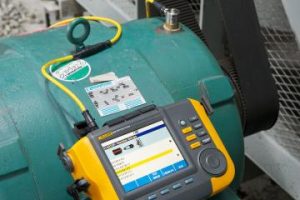
2. Misalignment of Components
Misalignment between the roller and other machine components can cause vibration. This issue often arises from improper installation or shifting of components due to operational stress. Misalignment can lead to uneven load distribution, increasing the likelihood of vibration.
3. Bearing Issues
Bearings support the roller and allow for smooth rotation. However, when bearings are worn out, damaged, or improperly lubricated, they can cause vibrations. Bearing issues may result from contamination, lack of maintenance, or incorrect installation.
4. Structural Resonance
Structural resonance occurs when the natural frequency of the machine’s components matches the frequency of external vibrations. This phenomenon can amplify vibrations, causing significant damage over time. Structural resonance is often associated with inadequate machine design or installation.
5. External Factors
External factors such as temperature variations, environmental conditions, and operational changes can also contribute to roller vibration. For instance, temperature fluctuations can cause thermal expansion or contraction, leading to imbalances and vibrations. https://industrialvibration.com.au/roller-vibrator/
Solutions for Reducing Roller Vibration
Addressing roller vibration requires a comprehensive approach that includes regular maintenance, proper installation, and use of advanced technologies.
1. Balancing the Roller
To address imbalances, it is crucial to balance the roller accurately. This can be done using balancing machines that detect uneven mass distribution and provide corrective measures. Regular inspections and cleaning can also prevent material buildup that contributes to imbalance.
2. Ensuring Proper Alignment
Proper alignment of machine components is essential to reduce vibration. This can be achieved through precise installation and alignment techniques. Regular checks and adjustments should be performed to maintain alignment, especially after maintenance or relocation of equipment.
3. Regular Bearing Maintenance
Bearings should be regularly inspected and maintained to prevent vibration. This includes ensuring proper lubrication, replacing worn-out bearings, and keeping them free from contaminants. Using high-quality bearings and following manufacturer recommendations can extend their lifespan and reduce vibration.
4. Addressing Structural Resonance
To mitigate structural resonance, it is important to conduct a thorough analysis of the machine’s design and installation. This may involve modifying the structure, adding dampers, or adjusting operational parameters to avoid resonance frequencies. Vibration monitoring systems can also help detect and address resonance issues.
5. Controlling External Factors
Managing external factors such as temperature and environmental conditions can help reduce roller vibration. Implementing climate control measures, such as heating or cooling systems, can minimize the impact of temperature fluctuations. Additionally, adjusting operational parameters to suit the environment can help maintain stability.
Advanced Technologies for Vibration Monitoring
Incorporating advanced technologies can significantly enhance the detection and management of roller vibration. Vibration monitoring systems, predictive maintenance software, and IoT sensors provide real-time data and insights, allowing for proactive maintenance and quick response to issues.
1. Vibration Monitoring Systems
Vibration monitoring systems continuously track vibration levels and detect abnormalities. These systems use accelerometers and other sensors to measure vibration frequencies and amplitudes. The data collected can be analyzed to identify trends and predict potential failures, enabling timely intervention.
2. Predictive Maintenance Software
Predictive maintenance software uses data analytics and machine learning to predict equipment failures based on vibration data. By analyzing historical and real-time data, these systems can forecast when maintenance is needed, reducing downtime and preventing unexpected breakdowns.
3. IoT Sensors and Data Analytics
Internet of Things (IoT) sensors are increasingly being used to monitor various parameters, including vibration. These sensors collect data in real time and transmit it to central systems for analysis. Data analytics tools then process the information, providing actionable insights for maintenance and optimization.
Conclusion
Understanding the causes and solutions of roller vibration is crucial for maintaining the efficiency and longevity of industrial machinery. By addressing imbalances, misalignment, bearing issues, structural resonance, and external factors, and incorporating advanced technologies, businesses can significantly reduce vibration-related problems. Regular maintenance, proper installation, and continuous monitoring are key to ensuring smooth and reliable operations.
By following these guidelines, companies can minimize downtime, extend equipment lifespan, and optimize overall performance. Implementing a comprehensive vibration management strategy not only enhances productivity but also ensures the safety and reliability of industrial processes.